A dynamic software model relying on sensor data called as “Digital Twin” refers to the digital support of external property that is useful for multiple purposes. The data from Sensors uses the Digital twins installed on external objects to represent their adjacent real-time status, working place or condition. It helps us to predict future and also to understand the present and the past operation. It is a very powerful tool which creates an impact on all business sectors.
The 3D model creates a virtual companion for the physical object, which is one of the examples of Digital Twin. It checks the status of the external object and projects an exact copy of the real one.
The Digital Twin concept is also called as “device shadow” as it copies the device’s state in present time. The digital twin must be up-to-date and clear in bringing forth the copy of the physical object’s states and properties, along with shape, gesture, angle, motion and status.
A Digital Twin is an artificial delegation of an object. It is useful in various applications like simulation, product design, monitoring, servicing, and optimization. It also paves way to the development of industrial Internet of Things (IoT).
The Four Dimensions of ERP Consolidation:
Digital twin discovered by CAD (Computer-aided design). In the early stages of product development the CAD uses software modeling which engineers and designers work with. The difference in a digital twin is that the demo has been maintained for following phases of the product’s life-cycle, such as maintenance and inspection.
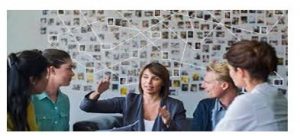
As reported by the product life cycle management (PLM) the digital twin concept requires three elements: in the real space the physical object must be present, in the virtual space its Digital Twin must be present, and the device which connects the two, stated expert Michael Grieves, who was amidst the first to use the term.
Extended Lifespan of Virtual and Real Worlds:
The virtual and actual products have increased their quality and amount of information and have progressed swiftly in the recent decade. The disadvantage is that there is no double-way connection between the two media and so they are lagging behind. Therefore the global manufacturers in present days work either with real products or virtual products.
They have not developed the connection between the two media so that they can handle it simultaneously. The common way to connect is to develop a fully defined 3D model. The manufacturing process developed by the global developers came to know about the design with a Manufacturing Bill of Materials (MBOM) and Bill of Process (BOP). The more advanced and complex manufacturers simulate the process of production automatically.
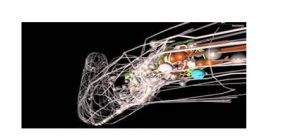
The Digital Twin is now being rapidly growing, and the idea of digital twin has also been implemented in the IoT sector. This technology has a high-level demand in immersive technique where it helps to link the physical and virtual world, thereby, enhancing the growth of this technology. There are various fields in which the Digital twin paves its way.