According to sources, the global 3D print market in 2015 was worth $ 192.9 million. Wohler’s and Associates rated the world’s 3D printing industry for 5,155 billion dollars, year. This means that 3D metal pressure is only 0.0% of the additive industry of 2015.
The major difference between the uses of the metal market value in comparison with other materials (that is plastic) is the only important barrier: the cost-effectiveness ratio. Grand View Research indicates that this important factor is the inevitable factor in the need for simple methods, with high costs and high costs to keep it clean.
In recent years, however, industry progress has made it clear that reducing the availability of raw materials as well as technological developments that increase sophisticated principles will have a higher market rate. These developments will reduce the growth of 3D metal production in 2025, worth $ 2.86 million, according to Research and Market Forecasts.
Aerospace industries
Most of the 3D applications of a metal display are Aeronautics (totaling a total of 3D metal printing costs of more than 35% in 2015). Frost & Sullivan’s Tech Vision report, research analyst Professor Ranjana Lakshmi Venkatesh Kumar says that “3D printing is very important in the aeronautics and automotive sectors” because of high power printing, low prototype, and low-cost printing capabilities. ”
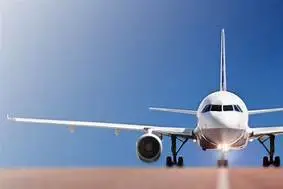
But more than prototypes, metallic 3D printing is more common for large-scale companies to implement directly in aircraft production. This year, Boeing will integrate titanium 3D printing into the production of 787 Dreamliner’s structural components. For the first time, this strategy allowed metal AM to be used in a real structure.
For the printing of titanium pieces, using traditional methods to manufacture fragments, the company will save 3 million dollars by plane. Additionally, GKN recently announced the major developments in the three aerospace metal production. This includes designing methods for large aircraft structures, such as frames as well as pressures for Saab working on their aircraft and research parts with the Oak Ridge National Laboratory.
Defense sector developments are usually due to civil applications in the next three years, so the investment of the defense sector is a powerful indication of 3D metal technology.
Automotive sector
As in the aerospace sector, rapid prototyping is historically the most common use of 3D technology in the automotive sector. Widespread acceptance of metal AM has not yet taken place in the automotive industry, as the sector is much more dependent on the mass production of parts than the aviation sector, which is considerably cheaper by using traditional manufacturing methods.
As a result of this limitation, the most appropriate applications for metal 3D printers in the automotive industry for high-end manufacturers, such as McLaren’s production of complex parts of Alumide. But there were clear steps forward to accept AM in production lines. For example, Father Systems has developed a liquid-based metal pressure process that will enable manufacturers to accelerate “3D printing rates to competitive conventional manufacturing processes,” according to their CEO Scott Vader.
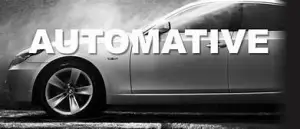
The University of Buffalo, which works with Father Systems, reports that they already have a lot of interest from one engine manufacturer for their machine, the MK1, who uses this process.
Although mass production through metal 3D printing is only in the early stages of its potential for widespread adoption in the automotive industry, it promotes overall growth in the industry.
Medical and Healthcare
The use of 3D printer software to produce healing support items with streamlined workflows, a fresh air.
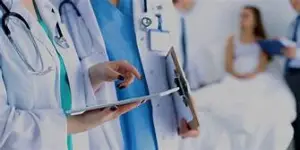
The 3YOURMIND platform allows medical staff implants and prosthetic devices based on existing scandal data by professional 3D service providers. The 3D-printed organic tissue is already part of scientific research.