The world of design and manufacturing has been completely transformed by 3D Printing, which can now print anything from jewelry to jet engines, shirts to shoes, and pianos to prosthetic limbs. Let’s go over the definition of 3D Printing once more before we plunge into the deep end. By adding successive layers of the desired material while using design data stored within a digital file, 3D Printing creates three-dimensional objects. The hardest part is creating the digital file, also known as a CAD file, which calls for computer design and troubleshooting expertise. On the other hand, the advantages of 3D Printing include a flurry of new manufacturing capabilities and a reduction in production costs.
1. Replicate Those Coral Reefs
Over the past few decades, the diversity of coral reefs has continued to decline, demonstrating the increasing fragility of underwater ecosystems. Many scientists are working to stop this loss by successfully printing reef structures that are then submerged in regions where there aren’t many corals. The coral specimen is then 3D printed as a small physical plaster model.
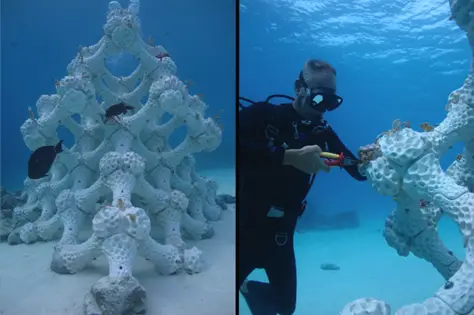
2. Emulating The Natural World
Biomimetics, also known as biomimicry or bionics, is the science that examines and applies ideas and concepts from nature to create highly effective products that enhance human life. The creation of Velcro is one of the most well-known uses of biomimicry.
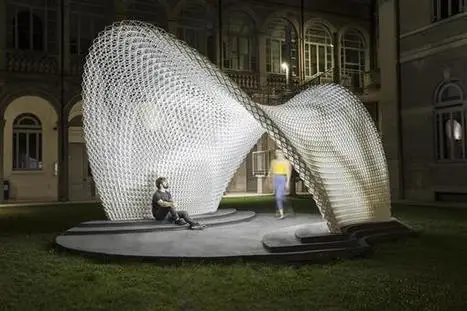
3. Module For Training Oceanographic Experimenters
In addition to technology, 3D Printing can be employed as a teaching tool for oceanographic researchers, particularly to examine the forms and structures of marine organisms. For instance, by examining square seahorse tails that were 3D printed, researchers discovered that square tails have better-grasping capabilities than cylindrical ones and are less likely to be damaged (deformed or fractured) under physical stress.
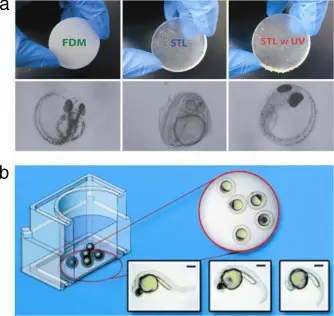
4. Utilized To Carry Out Different Mechanics
Additionally, various mechanics and physical load assessments have been carried out using 3D-printed models of variously shaped seashells. Analysis has uncovered new information regarding the development and evolution of intricate shell shapes in nature.
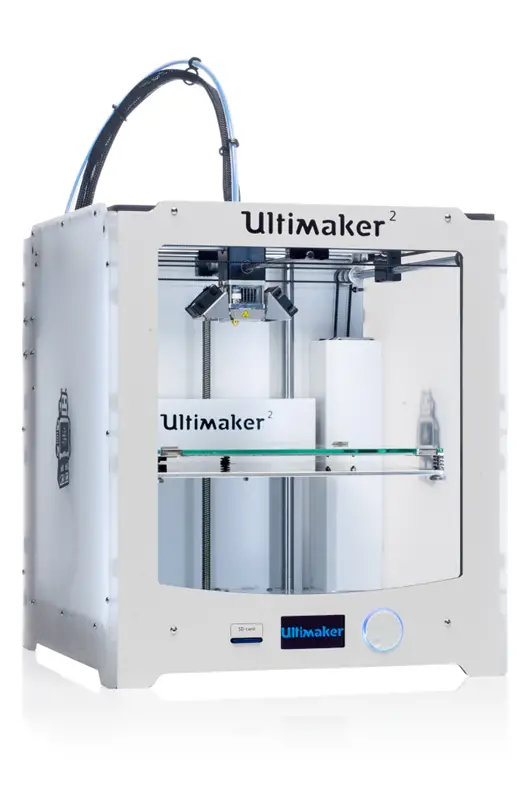
5. Spare Parts For Submarines Through 3D Printing
The US Navy knows the advantages of applying the technology in this way. The Navy announced that to reduce the strain on its supply chain, it would team up 3D printing companies with suppliers struggling to meet the demand to produce parts for its Columbia-class ballistic missile submarine program.
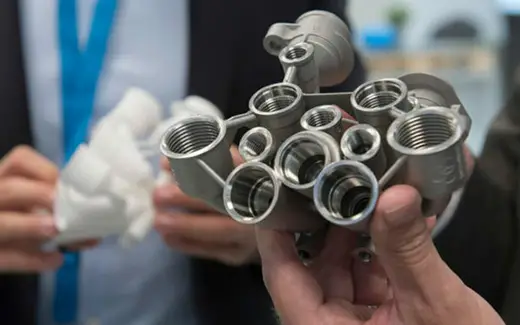
6. Creating An Arctic Seafloor Map
To speed up and lower the cost of mapping the Arctic seafloor, the Canadian company International Submarine Engineering (ISE) uses Sciaky’s 3D electronic additive manufacturing technology (EBAM). This ballast tank could be produced in 8 weeks instead of 16, thanks to 3D technologies! By following the ocean floor beneath the thick layer of ice, this autonomous underwater vehicle will be used to explore the Arctic.
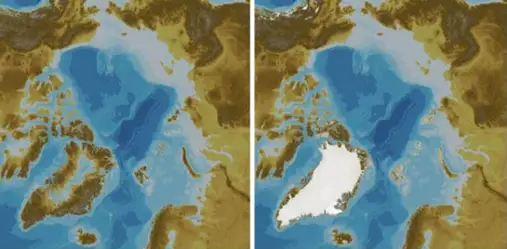
7. Chainmail For Ships 3D Printed
Chain mail is often thought of as an archaic form of armor, but NASA is resurrecting this more ancient weapon in a novel way. The chain mail, produced using 3D printing technology, has two sides: one that can reflect light and heat and the other that can take in heat and act as insulation. The use of this strong metal may be possible in a variety of space missions.
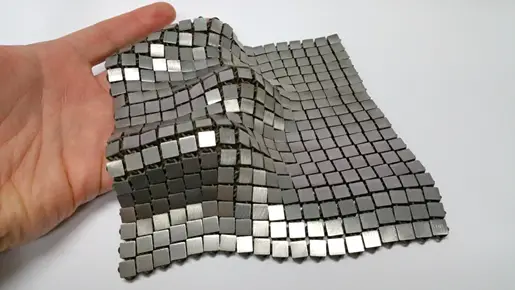
8. Missions Under The Sea Using 3D Printing
The manufacture of underwater equipment is another area where additive manufacturing is put to use, and ecoSUB Robotics is one marine technology company that has done so. The company is particularly interested in creating projects that can perform deep monitoring missions, are reasonably priced, and satisfy the requirements of both its commercial and military customers.
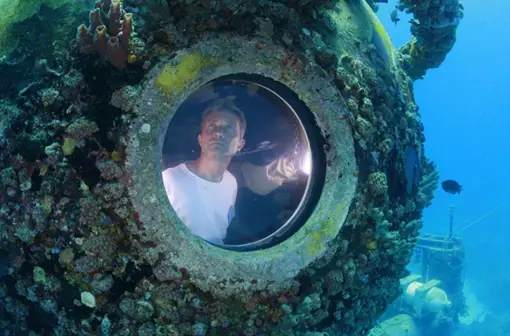
9. Metal Alloys For Maritime Use
The Newport News Shipbuilding division of Huntington Ingalls Industries and manufacturer 3D Systems have teamed up to deliver new metal materials that can be 3D printed for the maritime sector.
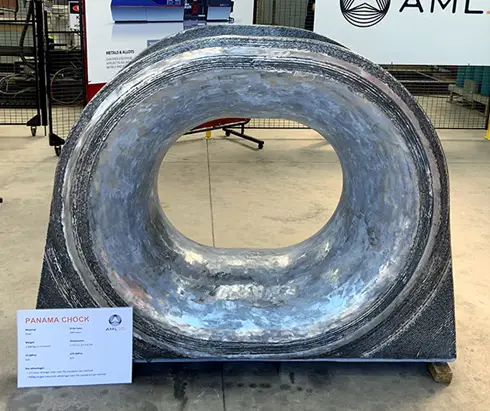
10. 3D Printing Enables More Environmentally Friendly Cargo Ships
Thomas Dahmen, a student researcher at the Technical University of Denmark, developed a 3D-printed injection nozzle earlier this year. Thomas Dahmen identified a way to enhance injection nozzles using the Quality Function Deployment (QFD) matrix, an analysis technique for assessing the potential advantages of additive manufacturing.
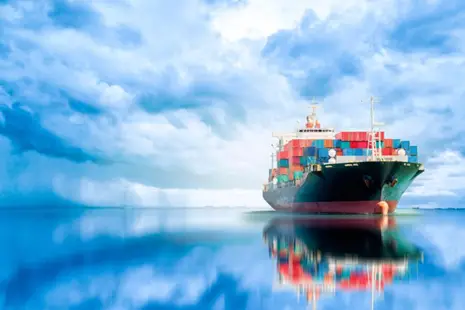