Handling sensitive computer components requires vigilance to prevent damage from electrostatic discharge (ESD). While robust systems have some built-in tolerance, accumulation of static can still cause issues over time or fail components entirely. Implementing diligent anti-static practices is essential for technicians and enthusiasts handling hardware outside of protective enclosures.
As outlined here through 10 key points, simple affordable tools and awareness of conditions can together provide an effective safeguarding regime. Across various diagnostic, upgrade, and repair procedures on desktops, laptops, servers, and embedded devices, hardware contacts should not carry static potential over 100-200 volts. Higher transient charges from operators can override protections degrade connectivity, and signal quality or destroy sensitive chips. Documented cases detail $20,000 server CPUs expiring from incidents while saving a $2 clamp is no comparison.
This analysis will examine straightforward measures DBAs, support analysts and hobbyists warrant through suitable tools and environment controls. We outline not just robust processes but inform operators on conditions influential across test cycles.
1. Use A Grounded Outlet
Regularly wearing an anti-static wrist strap dissipates charge safely away from components into the ground circuit. For consistent function, the earth point needs to connect via a power outlet or ground point meeting electrical standards. Verify ground integrity through an outlet tester before reliance, as many buildings have unwired sockets or lost continuity over time. Beyond wrist straps, standing anti-static mats also require proper grounding to operate effectively.
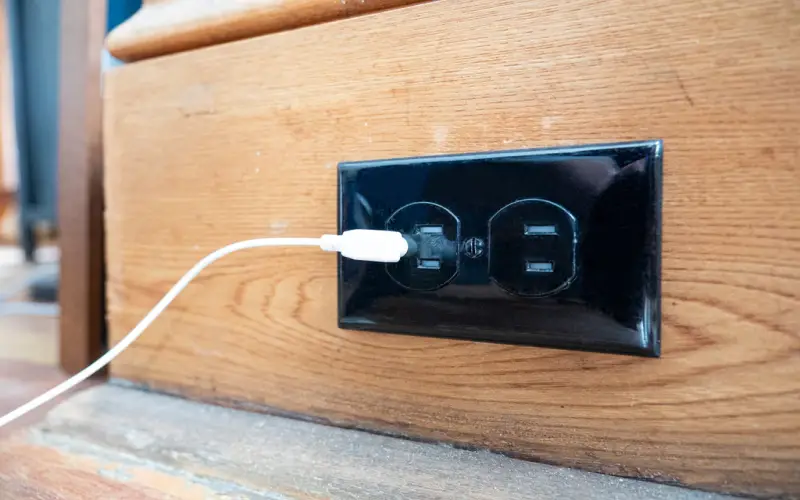
2. Wear An Anti-Static Wrist Strap
The simplest human contact safeguard involves a wrist strap with conductive band and ground cord. As the wearer builds static potential through movement or other environmental factors, the charge flows through the strap avoiding transfer handling. For under $10, accessories connect via crocodile clip or banana plug to dissipate directly through a verified grounded outlet or anti-static mat path to ground. Check strap condition over time watching for deteriorated bands or ground cords as metal component contact defeats protection.
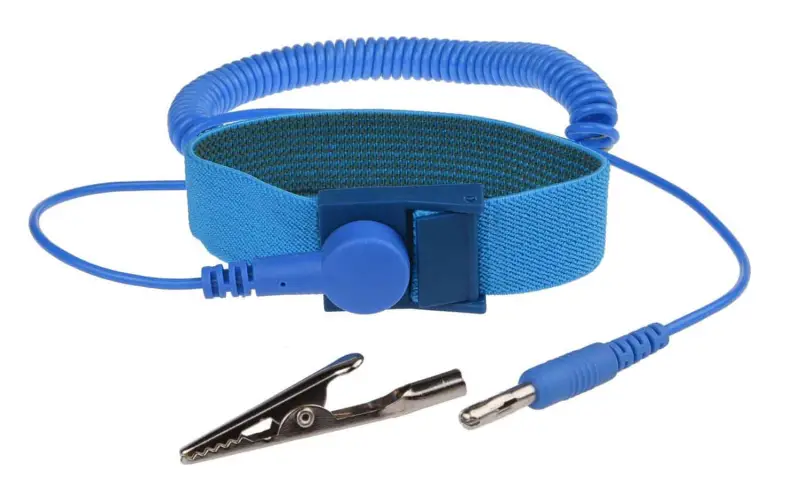
3. Avoid Synthetic Fabrics
Many cloth materials accumulate high static potential through friction contact. Electron exchange occurs most prominently with synthetics including nylon, polyester, and synthetic blends as examples. Avoid these unfavorable options choosing anti-static garments when possible or at least cotton materials if dedicated wear unavailable. Any engineers availing smocks or technician jackets should verify that anti-static thread and snaps are incorporated in the design.
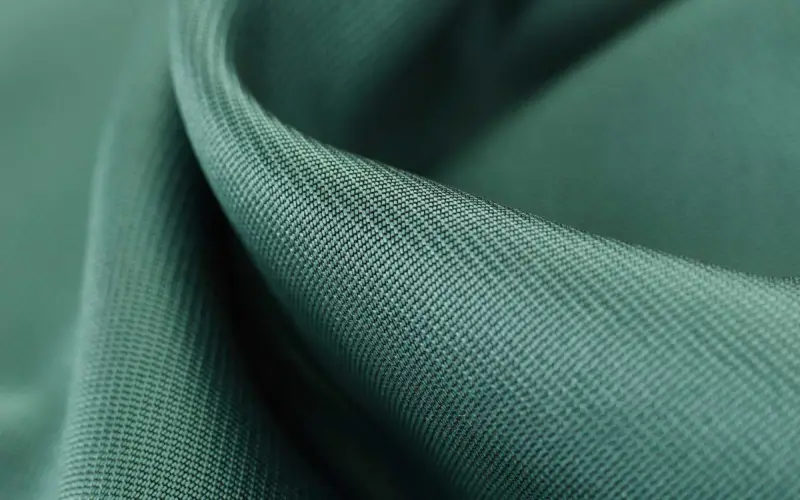
4. Maintain A Clean Environment
While environmental static sources warrant awareness, even workflow materials impact accumulation. Ensure hands, tools, and work surfaces are clean before handling boards and components. Wiping down areas with anti-static wipes or sprays neutralizes charge buildup while cleaning residues or particulates away. Technicians must then let surfaces dry completely before placing hardware to prevent liquid damage gaps. Meticulous cleaning limits liability conditions in general and static exposure during intricate handling.
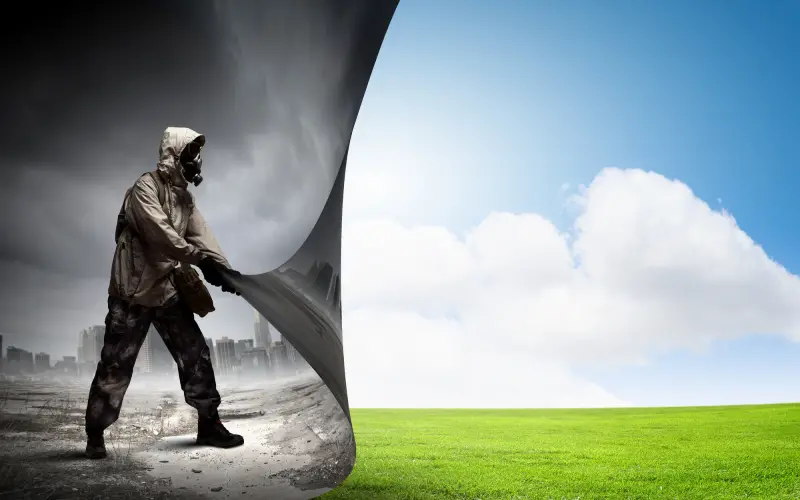
5. Use Anti-Static Bags
Board transport and temporary staging warrant anti-static precautions as well. Most sensitive computer components ship in anti-static bagging or foam providing a shield layer. Continue using these bags when moving devices or as temporary cover if interrupting repair. Certain bags rated for shielding can fully enclose hardware on the workbench or table. Also, consider anti-static foam or rubber mat options as an added layer protecting larger motherboards and expansions from surface charge beneath. Shielding prevents stray environmental energy from passing into sensitive components.
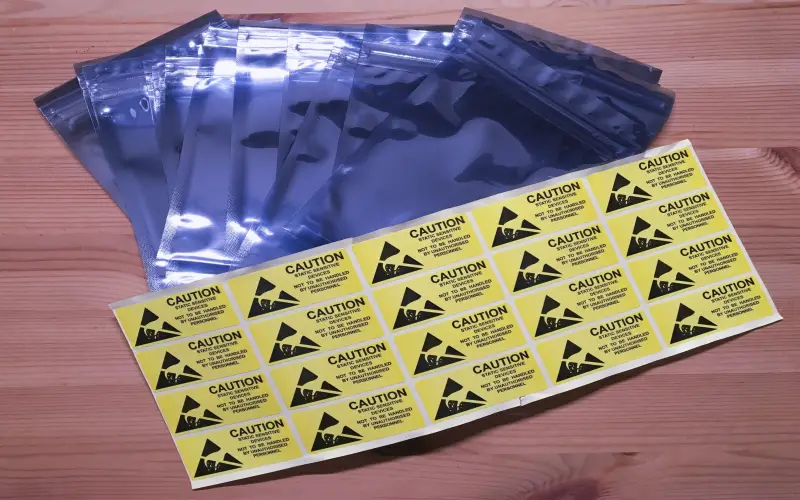
6. Use Anti-Static Sprays Or Wipes
In addition to providing cleaning properties, specially formulated anti-static solutions neutralize charge buildup from tools, garments, and environmental sources. Static dissipative sprays convert insulating surfaces while wiping films away, applied using spray bottles or pre-saturated wipes. Treat any questionable plastics or table spaces appearing to accelerate static shocks before mounting boards. Exercise care checking item chemical compatibility and avoiding oversaturation dripping into electronics. Periodic reapplication maintains effect as conditions dynamically change.
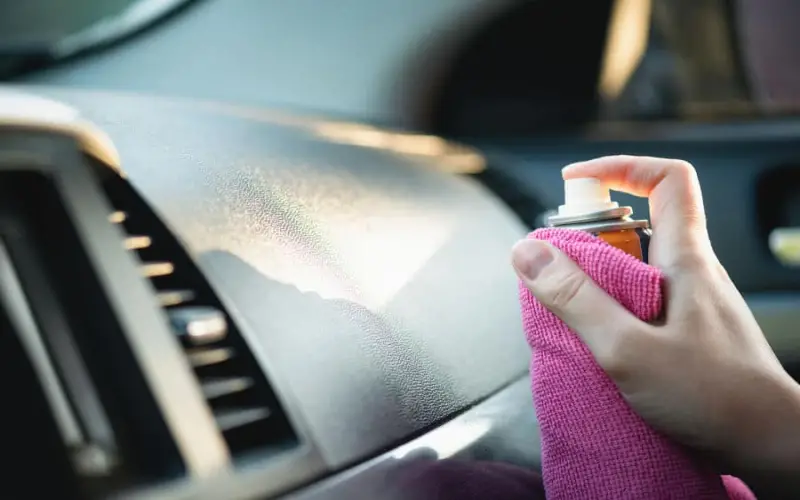
7. Work On A Flat, Hard Surface
A fundamental workshop element for hardware handling is the workbench, ideally featuring an ESD-safe laminate buildup. Metals and plastics accumulating stray static should be avoided as a primary surface foundation. Flat spaces allow stable precise manipulation without device shifting or incidental damage risk. Choose the hardest desks available as softer porous surfaces absorb solutions limiting ground plane continuity. Refinished timber desks contribute additional unknown resistance warranting insulation. Technicians shifting between locations should maintain rigid portable surfaces for temporary deployment.
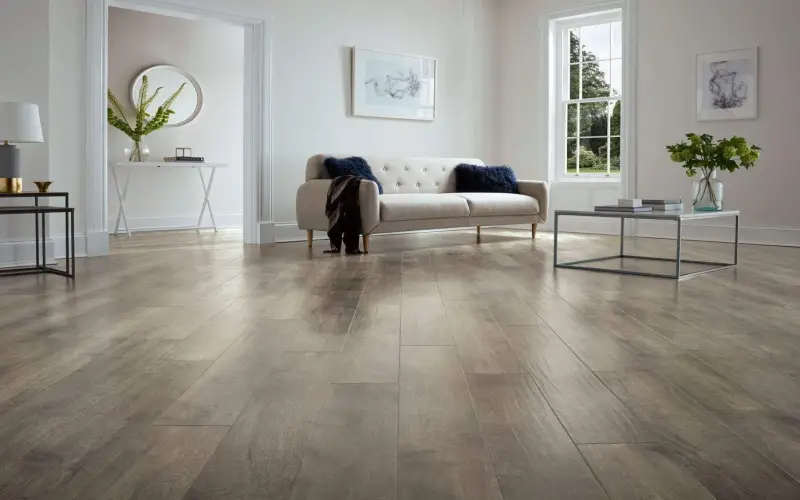
8. Avoid Touching Metal Parts
While working energized hardware risks like shorts are obvious, even unpowered handling warrants mitigation once boards are exposed. Any connectors, module edges, screw points, and shields represent local metalized paths subject to ESD damage. Handle plug-in cards exclusively by their largest shielded casings avoiding brushed points around ports or chip interfaces. This methodology avoids stray discharge paths across sensitive nodes. Unless measuring actively powered circuits, keep contact exclusively on cleaned exterior shells during manipulation.
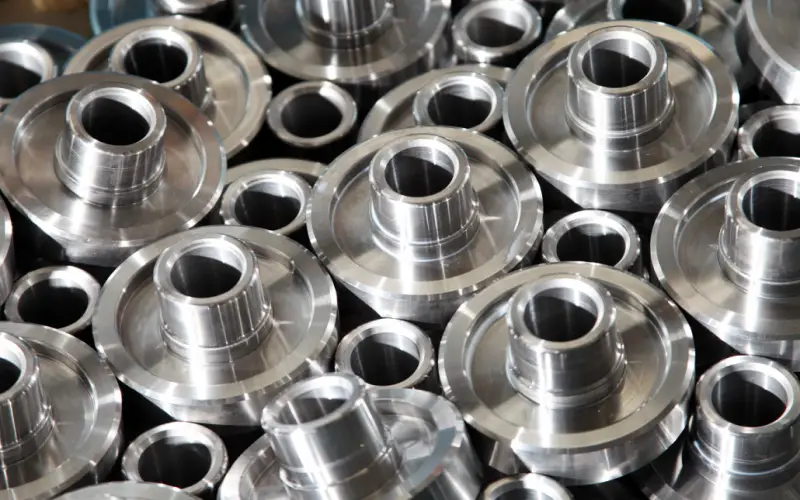
9. Keep Away From Static Sources
Recognizing and monitoring potential static sources in the workspace allows precautionary adjustment. Polyester lab coats, unrestrained plastic sheeting, and unchecked carpet fibers notoriously accumulate high static levels. Where such items prove necessary or unavoidable in business environs, increase ionizer usage while checking garment grounding consistency. Verify mechanical items like file cabinets, aluminum ladders or rolling bins are dissipative rated models before area use as unrecognized insulators easily capacitate dangerous potentials right in the workspace. Monitoring and checking less obvious energy reserves empowers sound workspace adjustments.
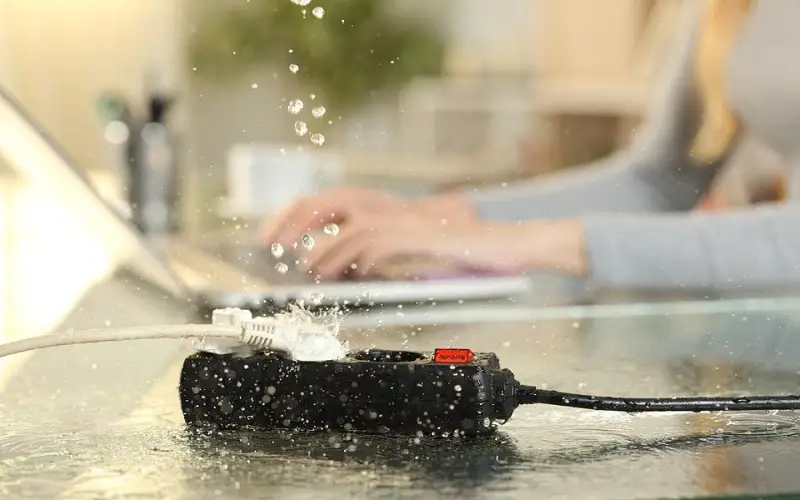
10. Be Aware Of Environmental Conditions
Weather and workspace humidity dynamically drive static generation reaching electronics. Cold winter months commonly see an uptick in ESD liabilities from garments and contact sources. Get in the habit of monitoring humidity levels across seasons making workspace regulation changes where warranted. As may be seasonally required, increase room humidifiers, floor and equipment wipe-downs, and wrist strap testing cycles should measurable resistors indicate below 40% room humidity. Careful condition awareness provides an advantageous adjustment opportunity over leaving the issue unchecked until equipment failures manifest.
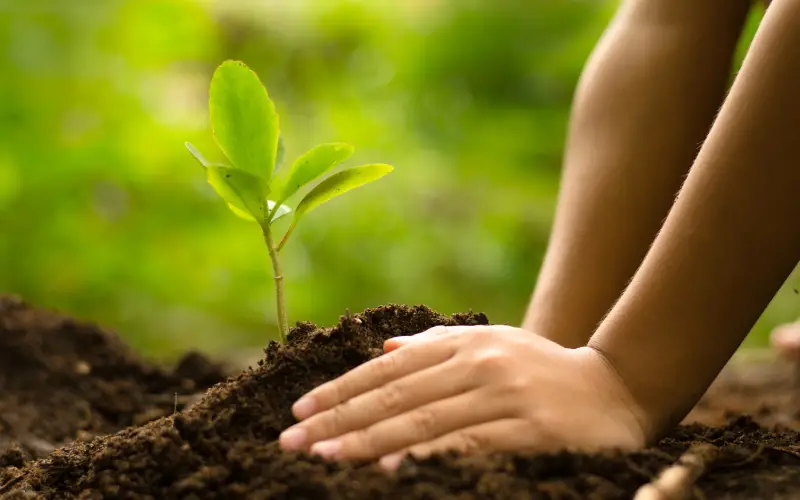