Using manual and cabled readings rather than wireless systems connected to digitized mining assets is a prominent signal of the industry unwillingness to digitize. There are several organizational impediments to novel notions like wireless readings, most notably mining’s reputation as a conservative, risk-averse business that discourages investment in potential technology. It is new for mines to use new technologies to increase productivity. Most leading mining companies have begun their digital journey, notably investing in autonomous and IoT-based technology.
1. AI And Analytics
Mining evolved into two sectors in one, integrating physical, and technical aspects. Digitalization and analytics enhance safety and boost reserves by lowering average site costs, extending mine life, and increasing NPV. Companies transition from empirical models to AI in day-to-day management and operations decision-making, the transition from relatively inflexible production planning based on long-term budgets to short two-week-horizon planning and improved agility across the value chain. They shift away from single-recipe, plug-and-play tools and towards numerous value-driven, built-for-purpose approaches adapted to unique requirements, away from strict workforce planning and towards more agile models with a multidimensional team working on the highest-priority areas.
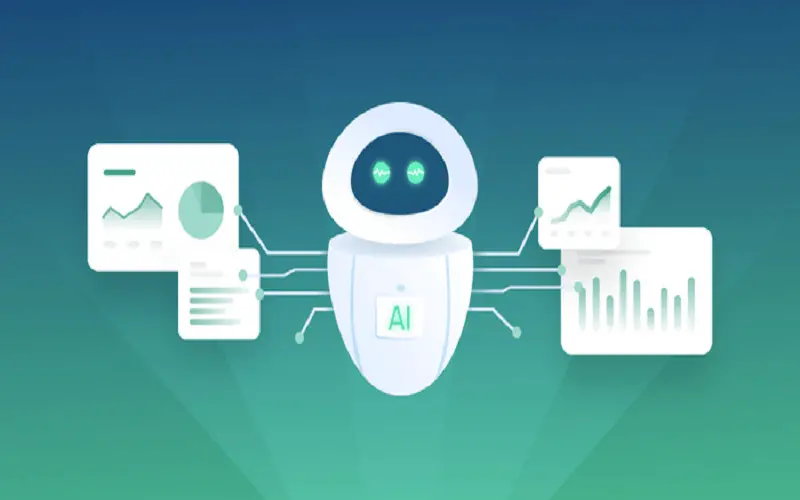
2. Develop Blockchain
Mining corporations are pioneering the use emerging technologies like blockchain for provenance and carbon-emissions tracking. Tracr, a blockchain network founded by De Beers, intends to monitor natural diamonds from the mine to the retail counter. MineHub and IBM have announced a collaboration to leverage blockchain technology to improve operational efficiency, logistics, and finance to cut costs in high-value mineral supply chain from mine to end buyer.
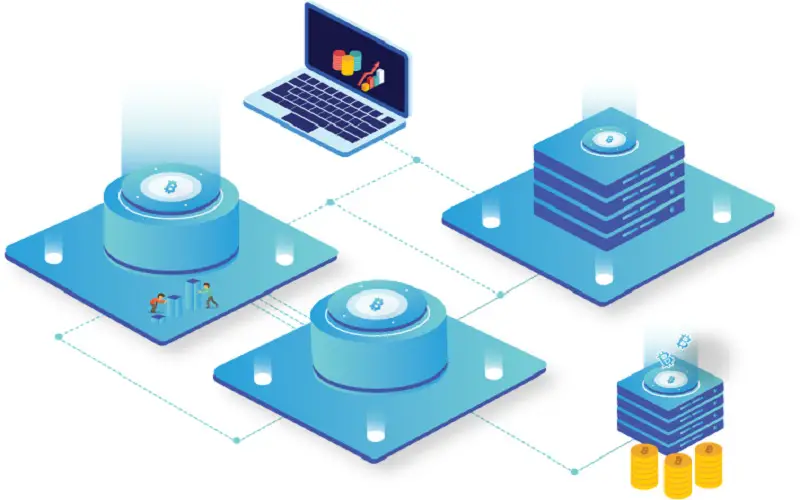
3. Machine Learning
One miner implemented predictive maintenance on their fleet using sensors and machine learning. The model predicted when elements fail, allowing a greater than 50% increase in the lifetime of essential components. The mining business is adopting machine learning, AI, and sophisticated data analytics to tackle business difficulties in prediction, categorization, and optimization.
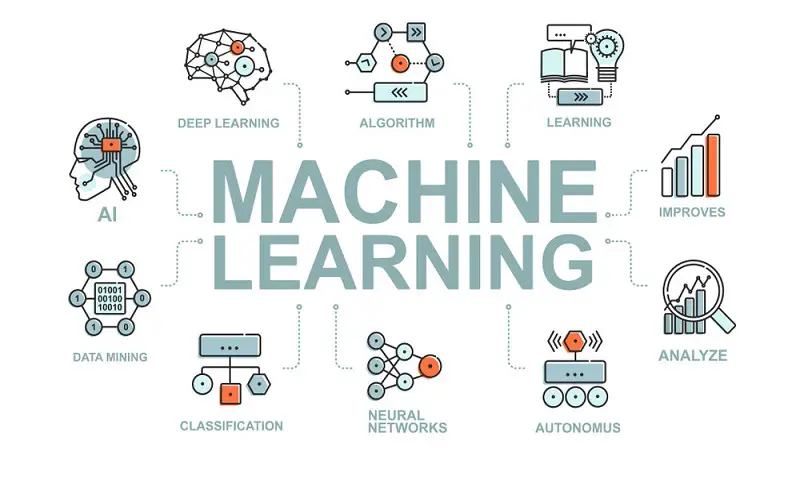
4. Predictive Asset Maintenance
The five most prevalent techniques for maintenance are reactive, preventive, condition-based, predictive, and prescriptive. Predictive maintenance extends the condition-based method by combining model-based anomaly detection, online sensing data collection, and data analytics to anticipate machine dependability. Data collected from IoT sensors assist mining businesses in understanding the health of assets in real-time, allowing them to forecast failure timings and employ condition-based maintenance to decrease costs, boost utilization, and prolong asset life.
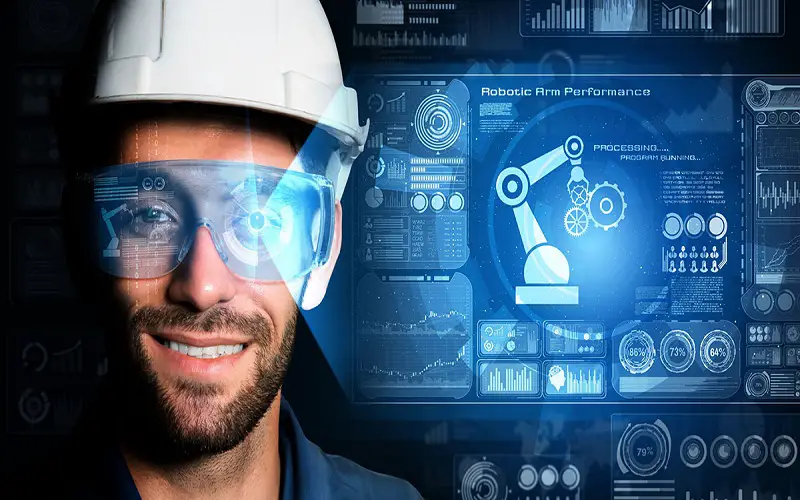
5. Database System
Query languages, query processing, optimization, and data model database systems are employed. Data analytics capabilities in recent database systems leverage data mining and warehousing approaches. Data warehousing collects historical data from different sources and merges it. It makes data cubes in a multidimensional database easier. The OLAP allows the creation of a multidimensional database. The mining task used to extend the database system requirements to improve capabilities and meet users needs.
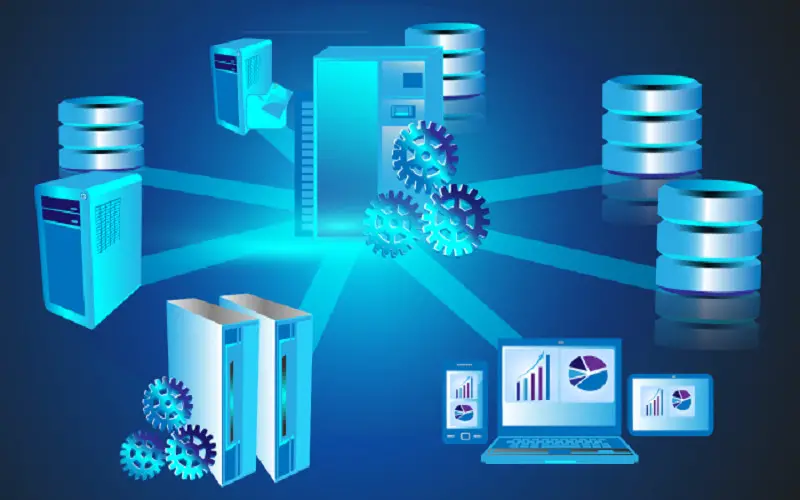
6. Statistics
Statistics linked to data mining. It investigates the gathering, interprets the data, and aids in the visualization of data display. Data classification and modeling is a statistical model utilized. It explains the behavior and probability of an object in a class. Data mining operations like categorization and data characterization produce statistical models. Statistics used to simulate noise and missing values in data. Statistics provides forecasting methods, predicting and summarizing data. Statistics help in pattern recognition. The statistical hypothesis was used for verification after mining a classification model.
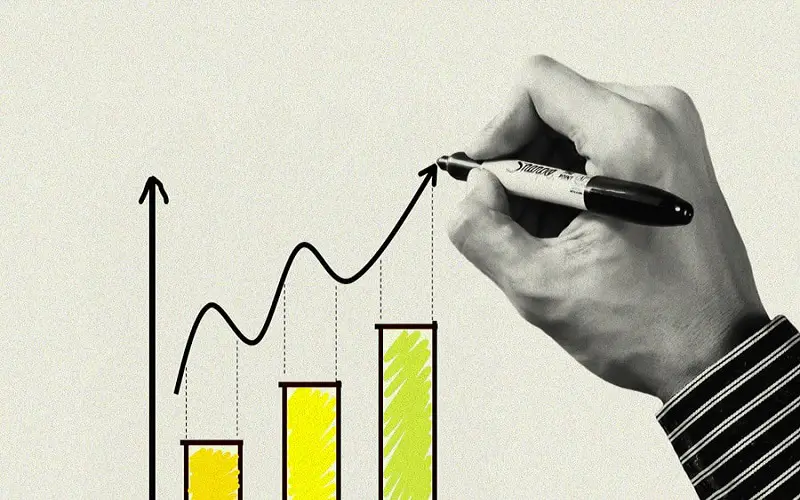
7. GPS Technologies
Global Positioning System Some mining firms have lately developed and installed satellite positioning and navigation systems on blast hole drills and electric cable shovels in their open-pit mines. The GPS devices generate precise, three-dimensional visualizations of the location of the drill bit and shovel tracks in real-time on a screen using a Moving Map Display. It enables the operator to steer the drill correctly from the blast hole and maintain a specific shovel grade and face position from a distant location. This system requires durable, established GPS components.
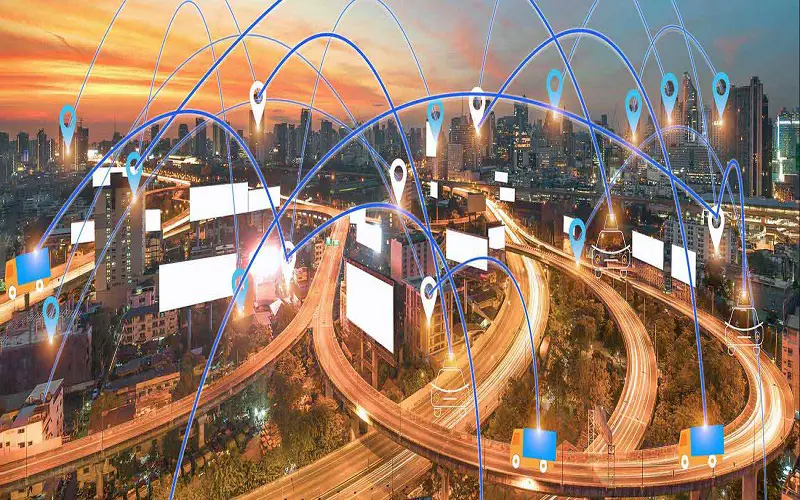
8. Wireless Monitoring
Mining assets are typically located in inaccessible regions, making manual readings by employees time-consuming and risky. When miners collect data and return to the office, the information obtained is outdated, and working with non-real-time data has serious consequences for mining operations. Pore water pressure in tailings dams shifts abruptly, exerting pressure on the infrastructure and potentially causing dam breakages, frequently with catastrophic effect. Operators reduce hazards by automating data collection operations with cabled readings. Installing cables across a mine infrastructure is costly, hard, and time-consuming.
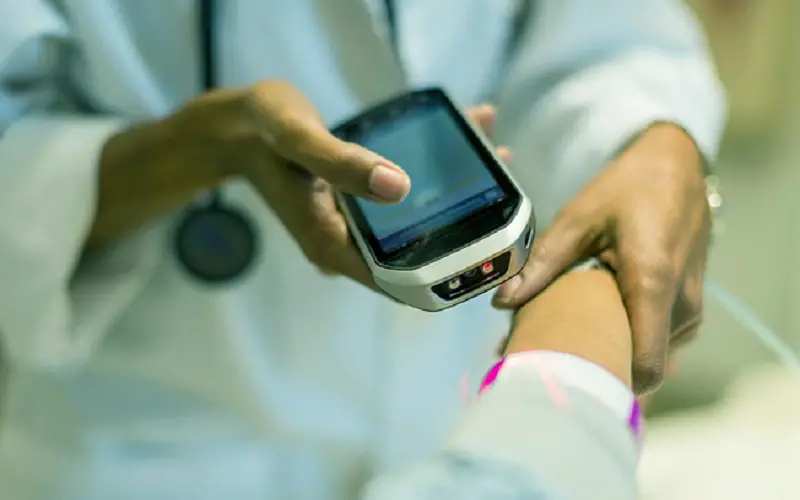
9. Workforce-Tracking
Wearable technology advancements make an attractive tool for mine crew tracking. It is beneficial in field maintenance and real-time machine inspection instructions, boosting operator-based care and safety, particularly in deep mines. RFID personnel tracking and staff visibility of staff enabled these devices, allowing essential workers to identified. They are used to identify areas where productivity is improved and track employee time and attendance. They reduce safety issues – and future tragedies – by restricting access to potentially problematic mine locations.
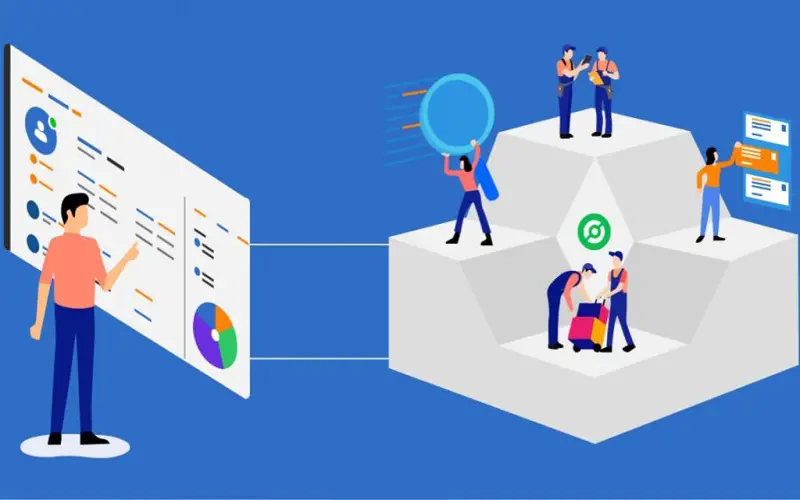
10. Automation
The vehicles transformed mining, allowing humans to communicate and operate machines remotely for the first time. Autonomous mining robots are semi-autonomous rather than automated, and they require human intervention in scenarios that they cannot manage on their own. The underground excavation vehicles are rendered autonomous by outfitting them with remotely operated tools and cameras, allowing users to conduct activities and see surroundings from a distance. The emphasis changed away from the initial autonomous mining trucks and towards the development of an independent mining system that carries out duties with limited external control, the prospect of full automation through robotic technologies.
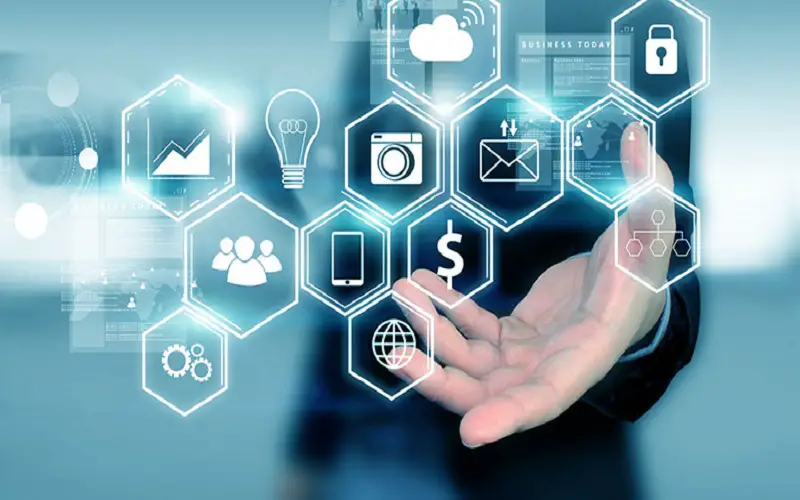