Six-Sigma –A Brief Introduction
Developed in the year 1981 by Motorola, US, Six Sigma is the term used to refer to the popular strategy of business management used in various industries today. It aims at improving the process output quality by first identifying and then eliminating the various causes of errors (defects), thereby reducing the variability in the business and manufacturing processes to the minimum.
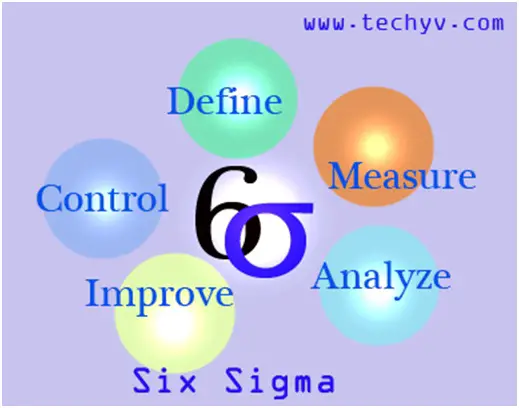
It employs various statistical methods and tools for quality management and develops a distinctive infrastructure of experts (‘green belt’, ‘black belt’, etc) within an organization. Every Six Sigma initiative has pre-determined financial targets and follows all the steps in a sequential manner.
The name ‘Six-Sigma’ has been derived from the terminology related to statistical modeling of the manufacturing processes. In manufacturing, the ‘sigma’ rating is generally used to describe a process’ maturity in terms of its total yield (percentage or number of defect-free items manufactured in the process). Precisely, a process wherein 99.99966 percent of the total number of products manufactured can be expected to be defect-free can be defined as the ‘Six-Sigma Process’. In other words, any process with 3.4 defects in every 1 million products manufactured is Six-Sigma in quality. Motorola was the first to use this concept to define the quality goal of all its manufacturing processes. Thereafter, it became a common goal to define quality in all engineering and management processes.
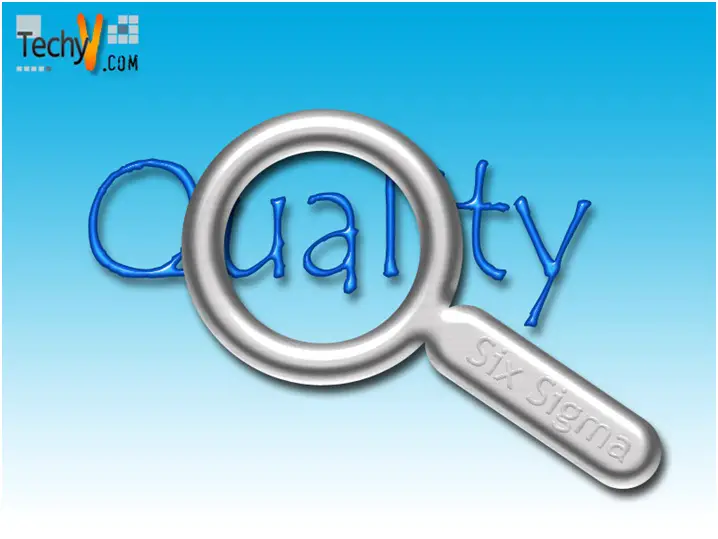
Six-Sigma Process – Basic Concept
The entire six-sigma concept is based on the idea that no item can fail to meet the specifications if 6 standard deviations are used between the nearest limit of specification and the given process mean. The calculations involved are largely derived from those used in process capability study. The process capability study measures the total number of std. deviations between mean and nearest limit in the sigma units. As the process mean begins to move away from tolerance center and as the std. deviation increases, sigma number gets reduced significantly, indicating an increase in the total number of defective items that do not meet the standard specifications.
Thus, as per the universally accepted definition, any engineering, management, or manufacturing process, which produces 3.4 DPMO (defective parts per million opportunities), is termed as a ‘six-sigma’ process. This definition is based on the basic fundamental that any normally distributed process is bound to have 3.4 ppm beyond 4.5 std. deviations below or above the process mean. Thus, if the ‘1.5 sigma shift’, caused due to prolonged variations, is to be excluded, six-sigma technically refers to 4.5 sigma units. This is important in assessing the quality of processes where the performance tends to get deteriorated with time as it eliminates the possibility of underestimating the practical defect levels.
Six Sigma Methodologies
The six-sigma approach follows 2 different project methods, which are derived from the PDCA Cycle given by Deming. Each of the 2 methodologies, DMADV and DMAIC, comprises of five phases.
DMAIC: It is best-suited for projects that aim at enhancing the performance of the existing business processes. This project method involves 5 methods – (i) Define customer voice, project goals, and problem. (ii) Measure primary aspects of exiting processes and gather relevant data (iii) Analyze gathered data to establish and evaluate cause-n-effect relations, (iv) Improve the existing process using techniques like mistake proofing, DOE, poka yoke, etc., and (v) Control future deviations to take preventive measures.
DMADV: It is best suited for projects that aim at developing new process or product designs. Also referred as ‘DFSS’ (Design for Six-Sigma), this methodology also comprises of 5 phases – (i) Define goals for design as per customer demand and organizational strategic goals, (ii) Measure and assess CTQs, risks, and product and process capabilities, (iii) Analyze data to create alternatives, develop high-level designs, and assess design capabilities, (iv) Design all details, optimize, and plan for verification of design, and (v) Verify created designs, pilot runs, and implementation.
Quality Management Methods & Tools Used in Six-Sigma Projects: Every phase in both the aforementioned methodologies requires certain quality-management methods and tools to be used. Some of the commonly used methods include histograms, ANOVA, QFD, 5-Whys, Axiomatic Design, Pick Chart, Pareto Chart, Chi-Square tests, Regression Analysis, correlation, run-charts, SIPOC analysis, cost-benefit analysis, Regression analysis, process capability, mapping of business processes, Taguchi methods, DOE, TRIZ, CTQ Tree, and FMEA, to name a few.
Primary Roles for Successful Six-Sigma Implementation
One of the main aims of Six-Sigma is to professionalize the various functions of quality management. Following are the primary roles assigned to experts within organizations to ensure successful implementation of Six-Sigma –
Executive Leadership: Responsible for establishing the vision for implementation of Six-Sigma and empowering people with other roles to explore and implement new ideas towards the overall vision. This category includes CEO and other senior top-management executives.
Champions: Their role is to ensure proper implementation of six-sigma in a well-integrated manner throughout the organizations. They are also expected to mentor the Black Belt holders.
Master Black Belts: Selected by the Champions, they serve as the in-house ‘six-sigma’ coaches, mentoring Green-Belt and Black-Belt holders. They are responsible to ensure that Six-Sigma is being applied consistently across all the departments in the organizations.
Black Belts: They are responsible for implementation of six-sigma methods in the specific projects assigned to them. They focus only on execution and report to the Master Black belt holders.
Green Belts: They are usually junior level executives, who take carry out implementation of Six-Sigma in a few projects apart from their usual job, under direct supervision of the Black Belt holders
Yellow Belts: They are employees who have the basic training of fundamental six-sigma methods and tools.
When & Where to Use Six-sigma?
Six Sigma approach must be used in the following cases:
Projects that involve unknown causes and situations
Projects that involve problems, which are not defined well and are very common.
Situations, wherein the ‘broad spectrum’ approach fails to improve quality or projects, wherein it is not possible to use the broad-spectrum approach
When other conventional quality improvement techniques fail
Complex business scenarios, involving multiple variables.
Six-sigma Importance – Why Do We Need It?
In the present scenario, the importance of Six-Sigma cannot be ignored. Organizations need it for the fact that it is much more important and efficient than any other conventional technique used to improve quality. The organizations that follow TQM principles emphasize on realizing the pre-established quality goals. This definitely helps in improving efficiencies, but prevents the organizations from tapping their potential to the maximum. Six-Sigma, on the other hand, helps to optimize the business processes fully by emphasizing on the need for consistent improvements in quality across all the functions in the organization.
Six-Sigma is imperative for all organizations for the following reasons –
Its Approach is Data-Driven: Six-Sigma methods employ statistical quality management techniques and tools to enhance quality and eliminate defects. This ensures accurate results based on figures and facts, which are very important in present-day’s complex business scenarios.
Enhances Customer Satisfaction & Helps Build Customer Loyalty – In today’s competitive world, it is important for business to consistently innovate and offer customers better quality services and products at competitive prices. Six-Sigma is needed as it can help the organizations achieve this objective and gain a competitive edge over their competitors. Enhanced quality of the offerings, in turn, leads to greater customer satisfaction, which helps in building customer loyalty over time. Having loyal customers is necessary for a business to ensure a persistent flow of revenue even at times of cyclical downturns in industry.
It follows a highly structured approach, enabling the employee to implement the technique in the projects accurately, without missing on any important step.
As the benefits are quantified by using six-sigma, it becomes easier for senior managers to assess the loopholes and bring about the necessary improvements.
It offers sustainable solutions.
It emphasizes on selecting and managing the right problem with the help of project selection matrices.
Proven method of quality improvement in all kinds of deployments.
It has the inherent ability to involve and guide teams through simulation exercises, thereby ensuring desired results in stipulated time.
It helps in implementing recommendations from senior management in a structured manner, ensuring a very high success rate.
Thus, Six Sigma is extremely essential to achieve quality goals in present-day business scenarios and cannot be ignored if the organization is willing to retain its position in the industry and ensure sustainable development.